切削加工過程中所採用的切削速度、切削深度和進給量等工藝參數,又稱切削資料。如圖所示,切削速度v(米/分)表示工件被切削表面與刀刃之間的相對運動速度;切削深度ɑp(毫米)表示在垂直於切削速度與進給方向所組成的平面內測量的車刀與工件的接觸量;進給量有3種表示方法:①每分鐘進給量vf/sub>(毫米/分):表示每分鐘內工件與刀具之間的相對位移量,②每轉或每行程進給量f(毫米/轉或毫米/雙行程):表示每轉或每次往復行程中工件與刀具間沿進給方向的相對位移量,③每齒進給量ɑf(毫米/齒):表示多齒刀具相鄰兩齒與工件接觸的時間間隔內,工件與刀具的相對位移量。3種進給量之間的關系如下式
vf=f·n=ɑf·z·n
式中 n為工件或刀具的轉速(轉/分)或每分鐘行程數(雙行程/分); z為多齒刀具的齒數。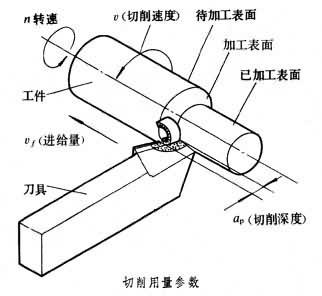
正確選擇切削用量,對於保證加工質量、提高加工效率和降低生產成本具有重要意義。選擇切削用量時應考慮的主要因素有:刀具和工件的材料、工件的加工精度和表面粗糙度、刀具壽命、機床功率、機床-機床夾具-工件-刀具系統的剛度以及斷屑、排屑條件等。最早研究切削用量的是美國人F.W.泰勒,他從1880年開始對單刃刀具的切削進行瞭26年(5萬次)科學試驗,總結出切削用量與刀具壽命、機床功率和切削液等因素相互影響的規律,從而推動瞭當時機床和刀具技術的重大改革。此後,不少國傢在試驗研究和生產實踐中積累的典型切削數據大多匯編成冊,供操作人員查閱和參考;或把這種大量數據存儲在電子計算機中成為切削數據中心(庫),可為用戶隨時提供切削用量方面的咨詢服務。
與某一工序的切削用量有密切關系的刀具壽命(見金屬切削原理),一般分為該工序單件成本最低的經濟壽命和最大生產率壽命兩類。按前者選擇的切削用量稱為最低成本切削用量,這是通常使用的;按後者選擇的切削用量稱為最大生產率切削用量,一般在生產任務緊迫時使用。
用硬質合金車刀車削碳素鋼時,刀具壽命與切削用量的關系可用如下的經驗公式表示
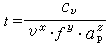