利用相似性原理實現多品種、中小批量高效率生產的生產技術和管理技術,英文簡稱GT。它是在零部件通用化、標準化的基礎上採用系統理論的思想和方法而建立的(見管理工程)。成組技術突破瞭傳統的以產品為物件的批量概念和生產技術組織方法,也打破瞭產品之間的界線。在多品種、中小批量生產的機械製造企業中,各種產品的零件可按形狀、尺寸、材料和工藝的相似性歸類分組,在歸類分組的基礎上組織各項生產活動。例如,設計部門可根據零件形狀特徵把圖紙集中分類,通過標準化減少零件種類,縮短設設計時間,並可存儲在計算機內為計算機輔助設計(CAD)創造條件。加工部門可將零件按形狀、尺寸和加工技術的相似性組成加工組,按照加工工藝的共同規律,采用專用工夾具在高效專業化的機床上或生產線上組織生產,並為實現計算機輔助制造(CAM) 奠定基礎。成組技術在多品種、中小批量生產企業中具有重要意義,有利於促進產品結構的系列化、部件的通用化和零件的標準化,擴大生產批量和先進技術的應用范圍,合理組織生產技術準備工作,改善生產組織計劃管理和保證產品質量等。
簡史 成組技術的概念是20世紀50年代由蘇聯С.П.米特羅法諾夫提出的。當時中國稱之為成組加工,即按工序成組。各類產品的零件按工序相似性,分別安排在不同的組內加工,突破瞭批量的制約。60年代初,這種方法引起歐洲的一些專傢的註意,並作瞭進一步的研究和應用,逐漸由工序成組發展到整個工藝過程成組,中國稱之為成組工藝。在這一階段,英國提出生產單元(cell)的概念,捷克斯洛伐克和聯邦德國提出零件分類編碼系統。70年代,各國開始把成組技術用於產品設計、生產技術準備、工藝設計和生產管理等方面,以成組技術為基礎進行計算機輔助設計、計算機輔助工藝過程編制(CAPP)和計算機輔助制造。這時,成組技術開始進入鑄、鍛、沖、焊、熱處理和裝配等領域,成組的概念進一步得到擴大和發展。各工業發達國傢大力從事以成組技術為基礎、以系統工程為方法的CAD/CAM系統的研究,產生瞭柔性制造系統(FMS)和計算機輔助工程制造系統,成組技術發展到一個更高級階段,使多品種、中小批量生產也能實現高度自動化,生產率大幅度提高,靈活適應多品種的變換,使生產方式出現瞭新的變革。
60年代初期中國開始試行成組加工。70年代開始成組技術的研究和應用。80年代開始研究和設計中國的零件分類編碼系統。
零件分類編碼系統 在機械制造的全部生產過程中有鑄造零件、沖壓零件、鍛造零件、機械加工零件和熱處理零件等的分類編碼系統。
機械加工零件的分類編碼系統有聯邦德國的奧匹茲(Opitz)系統,英國的佈裡奇(Brisch)系統,荷蘭的米克拉斯(Miclass)系統,日本的KK系統等。分類編碼系統的作用是:①提供各種重要的統計信息;②對零件信息進行標識;③對產品設計和工藝設計進行檢索和標準化;④便於使用電子計算機進行編碼、檢索、處理各種信息和建立數據庫,並有助於計算機輔助設計、輔助制造和輔助生產管理;⑤便於機械加工零件的分類分組。中國在1982年制定瞭機床零件分類編碼系統(JCBM-1),1984年又制定瞭機械工業零件分類編碼系統(JLBM-1,見圖)。
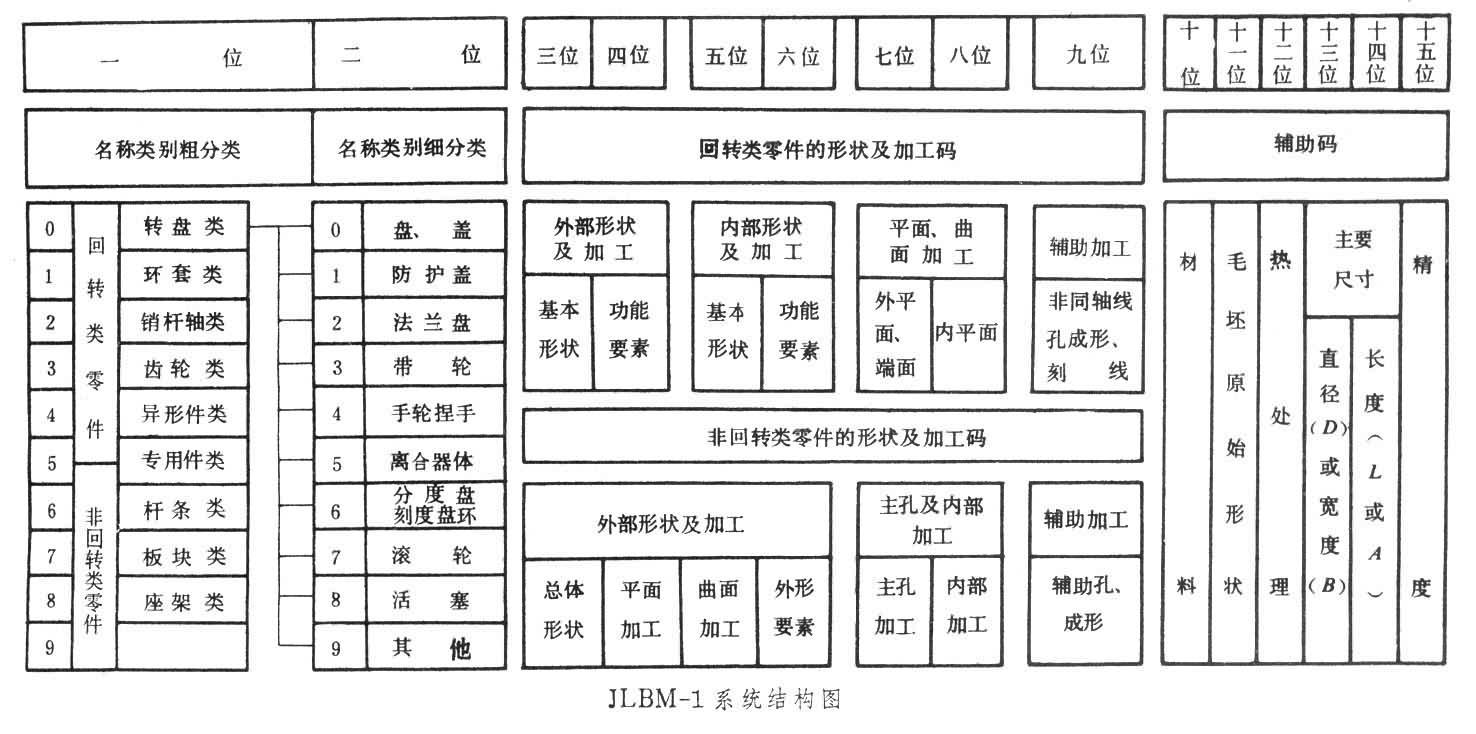
成組技術條件下的產品設計 用成組技術原理進行產品設計的核心是將零件通過編碼按相似性分組儲存,供設計新產品時檢索,以促進零件的系列化、通用化和標準化(簡稱三化)。從零件三化到部件三化,最終達到模塊化設計,從而加強產品設計和產品的更新速度,提高產品的競爭能力。設計人員通過微縮膠片、穿孔分卡片等檢索出所需零件並進行復制,從而減少設計工作量。在計算機輔助工程制造系統中,通過人機對話、實現計算機自動計算並自動繪制零件圖紙。
成組工藝設計 包括成組鑄、鍛、沖、熱處理、機械加工、裝配等部門的工藝設計。通常采用復合零件法和復合工藝法來制定成組工藝規程,這兩種方法都綜合瞭工藝相似零件組內各種零件的全部結構特征和工藝特征,因此成組工藝規程設計不但適用於加工組內任何一種零件,也適用於能進入該加工組的新零件。成組工藝設計能使企業多數零件之間具有工藝上的繼承性和相關性。
成組夾具 在成組加工中針對一組零件的某道工序或流水生產線上的多道工序而設計的可調夾具。它的主要特征是具有適應同組零件連續生產的柔性。夾具由固定不變的夾具體和可換或可調整的夾持元件等組成。當用成組夾具加工完一種零件並轉換加工同組內另一種零件時,不需要更換設備上的夾具體,而僅更換夾具體上某些定位和夾緊元件就可以加工。采用成組夾具可代替大量的專用夾具,節約生產準備時間和設計、制造專用夾具的時間和費用。
成組加工機床 零件成組後,成組批量比原來的批量擴大很多,因此可以經濟有效地采用可調的高效機床或數控機床進行加工,迅速提高生產效率。成組加工機床的主要特征是具有適應同一加工組內所有零件的連續生產柔性。因此傳統的機床設計結構也因之發生變化。數字控制機床、加工中心等先進設備就能在成組加工或中小批量生產中得到廣泛的應用。
成組加工的組織形式 成組加工的生產組織形式一般有成組單機、成組生產單元和成組流水線。
① 成組單機:在一臺機床上能完成工藝相似零件組全部或多道主要工序。這種形式可以減少工序間停頓和調整時間,對提高機床利用率和生產效率有明顯的效果。
② 成組生產單元:在工作場地內配置可以完成工藝相似零件組內所有零件全部工序所需的不同類型的機床。生產單元的生產任務、加工方法、設備和工藝裝備基本上是固定的,所以能簡化生產管理,有利於提高產品質量和生產效率。同一類工藝相似零件的不同工序在一個生產單元內全部完成,可以縮短零件的運輸路線和生產周期,減少在制品。
③ 成組流水線:工作場地內的機床是按照工藝相似零件組的復合工藝過程的順序佈置的。成組流水線具有足夠的柔性,並要求工藝相似零件組內的零件有很強的工藝相似性和較大的生產批量。這種形式具有大量流水線的多種特征和優點(見大量生產技術)。
成組生產作業計劃 推行成組技術,按相似零件組組織生產便能打破產品界限,改變傳統的按產品組織生產的方式。對相似零件、特殊零件一般采用單一生產間隔期的定期不定量生產方法;對結構簡單、價值低的標準件、通用件一般采用定量不定期的生產方法,也稱定貨點法(見庫存管理、期量標準、生產作業計劃)。
為瞭給編制生產作業計劃提供依據,企業要編制生產間隔期的生產計劃。它是根據年度生產計劃和短期市場預測而編制的。各生產單元應選擇同一的生產間隔期,並盡可能縮短。生產間隔期短,在制品占用量少,對市場變化的適應性強,但也帶來調整時間損失的增加,因此選擇時應權衡利弊。生產單元的每一生產間隔期應成套生產一個批量的工藝相似零件組中的所有零件。這些零件的產量應在投入提前期開始下達,以便各成組生產單元對所承擔的產品的所有零件進行全面考慮,對所用工具相同、調整方法相似的零件依次進行加工,並進行優化排序。這種方法能夠較好地處理成組加工和零件配套、擴大生產批量和減少在制品占用量的關系,從而在簡化管理、提高生產效率、縮短生產周期、減少在制品占用量、保證生產負荷平衡等方面發揮成組技術的優勢。