利用浸在工作液中的兩極間脈衝放電時產生的電蝕作用蝕除導電材料的特種加工方法,又稱放電加工或電蝕加工,英文簡稱EDM。
簡史 電火花加工於1943年由蘇聯學者 Б.Ρ.拉紮連科夫婦研究發明後,隨著脈衝電源和控制系統的改進而迅速發展起來。最初使用的脈衝電源是簡單的RC(電阻-電容)回路。50年代初,改進為RLC<(電阻-電感-電容)等回路。同時,還采用脈沖發電機之類的所謂長脈沖電源,使蝕除效率提高,工具電極相對損耗降低。隨後又出現瞭大功率電子管、閘流管等高頻脈沖電源,使在同樣表面粗糙度條件下的生產率得以提高。60年代中期,研制成晶體管和可控矽脈沖電源,提高瞭能源利用效率和降低瞭工具電極損耗,並擴大瞭粗精加工的可調范圍。到70年代,出現瞭高低壓復合脈沖、多回路脈沖、等幅脈沖和可調波形脈沖等電源,在加工表面粗糙度、加工精度和降低工具電極損耗等方面又有瞭新的進展。在控制系統方面,從最初簡單地保持放電間隙而控制工具電極的進退,逐步發展到利用微型計算機對電參數和非電參數等各種因素進行適時控制。
加工原理
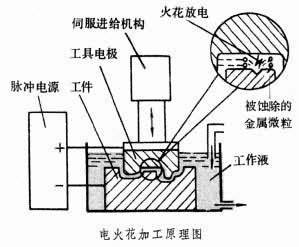
種類 按照工具電極的形式及其與工件之間相對運動的特征,可將電火花加工方式分為5類:①利用成型工具電極相對工件作簡單進給運動的電火花成形加工;②利用軸向移動的金屬絲作工具電極,工件按所需形狀和尺寸作軌跡運動以切割導電材料的電火花線切割加工;③利用金屬絲或成形導電磨輪作工具電極進行小孔磨削或成形磨削的電火花磨削;④用於加工螺紋環規、螺紋塞規、齒輪等的電火花共軛回轉加工;⑤小孔加工、刻印、表面合金化、表面強化等其他種類的加工。
特點和應用 電火花加工的主要特點是:①能加工普通切削加工方法難以切削的材料和復雜形狀工件;②加工時無切削力;③不產生毛刺和刀痕溝紋等缺陷;④工具電極材料無須比工件材料硬;⑤直接使用電能加工,便於實現自動化;⑥加工後表面產生變質層,在某些應用中須進一步去除;⑦工作液的凈化和加工中產生的煙霧污染處理比較麻煩。
電火花加工的主要用途是:①加工具有復雜形狀的型孔和型腔的模具和零件;②加工各種硬、脆材料如硬質合金和淬火鋼等;③加工深細孔、異形孔、深槽、窄縫和切割薄片等;④加工各種成形刀具、樣板和螺紋環規等工具和量具。
參考書目
北京金屬切削理論與實踐編委會編:《電火花加工》,北京出版社,北京,1980。