內部或外部承受流體壓力並對安全性有較高要求的密封容器。壓力容器早期主要應用於化學工業,壓力多在10兆帕以下。隨著化工、石油化工、煤化工等流程工業的發展,核能、海洋與航太等新興工業領域的出現,以及設計、材料、製造與檢驗技術的不斷進步,不僅促使壓力容器的壓力、溫度、容量範圍不斷擴大,還要求壓力容器能承受各種苛刻工況條件下的腐蝕。如人造水晶、高壓聚乙烯所用的壓力容器達100兆帕以上,煤化工要求壓力容器的單臺重量達到數千噸,現場製造的球形壓力容器、預應力混凝土壓力力容器直徑可達數十米,海洋工程需要能在水下幾千米工作的外壓容器。
壓力容器是具有爆炸危險的特種承壓設備。許多壓力容器中有易燃、易爆、有毒介質,一旦發生事故會誘發火災、化學爆炸及環境污染等惡性後果。核電站用反應堆壓力容器如發生事故,就會使放射性物質外逸,造成更為嚴重的後果。因此,防止壓力容器發生事故,始終是壓力容器設計、制造和使用者首要的任務。為使壓力容器在確保安全的前提下達到設計先進、結構合理、便於制造、使用可靠和制造經濟等目的,各國都根據本國具體情況制定瞭有關壓力容器的標準、規范和技術條件,對壓力容器的材料、設計、制造、安裝、使用、檢驗及修理改造等各個方面提出具體和必須遵守的規定。
結構 壓力容器主要為圓筒形,少數為球形或其他形狀。圓筒形壓力容器通常由筒體、封頭、接管、法蘭、密封及支座等零件和部件組成。圖1中的壓水堆核電站反應堆壓力容器是一種典型的圓筒形壓力容器。壓力容器的筒體有多種結構形式,屬於整體式的有單層卷焊、鍛焊等,屬於組合式的有多層包紮、熱套、扁平繞帶等。
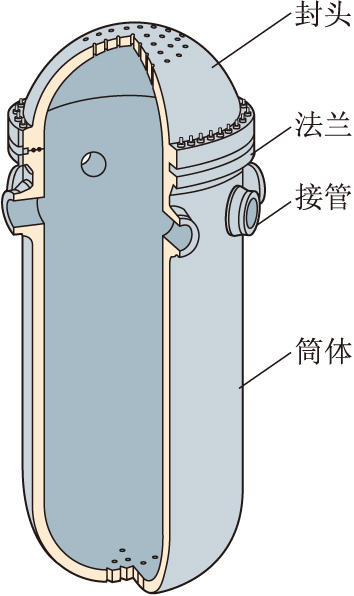
單層卷焊式壓力容器 用鋼板卷焊成筒節,再將筒節焊制成筒體。它是制造工藝最簡單,應用最廣泛的筒體結構形式,多層包紮、扁平繞帶的內筒以及熱套的各單層筒都是采用這種結構制造的。由於受鋼板生產、卷制能力的限制,其厚度一般不超過300毫米。
鍛焊式壓力容器 由鍛造的筒節經組焊而成,結構上隻有環焊縫而無縱焊縫。20世紀70年代以來,由於冶煉、鍛造和焊接等技術的進步,已可供應570噸重的大型優質鋼錠,並能鍛造最大外徑為10米、最大長度為4.5米的筒體鍛件,因而大型鍛焊式壓力容器得到瞭發展,成為輕水反應堆壓力容器、石油工業加氫反應器和煤轉化反應器的主要結構形式。
多層包紮式壓力容器 在20世紀30年代就已開始在工業上使用(圖2)。這種結構壓力容器的內筒厚度一般為12~25毫米,外層層板的厚度一般為6~16毫米。這種結構的優點是材料的選用有較大的靈活性,可按介質的腐蝕性選用合適的內筒材料,而層板選用一般壓力容器用鋼。
扁平繞帶式壓力容器 采用傾角錯繞的方式將扁平鋼帶纏繞於內筒上,使筒體上的扁平鋼帶層既能承受切向力也能承受軸向力。內筒的厚度一般為筒體總厚度的1/6~1/4,扁平鋼帶式壓力容器是中國首創的一種高壓容器,在小化肥生產領域獲得瞭廣泛的應用。
熱套式壓力容器 內筒外面套合上一至數層外筒,組成筒節。通常先將外層筒體加熱使其直徑增大,以便套在內層筒體上,冷卻後的外層筒體就能緊貼在內筒上,同時對內筒產生一定的預加壓縮應力。內筒和外筒的厚度一般相同,常用25~50毫米的鋼板卷焊而成。熱套壓力容器用的鋼板比其他多層壓力容器的層板厚,層數少(一般2~3層,最多為5層),所以生產效率比其他多層壓力容器高。
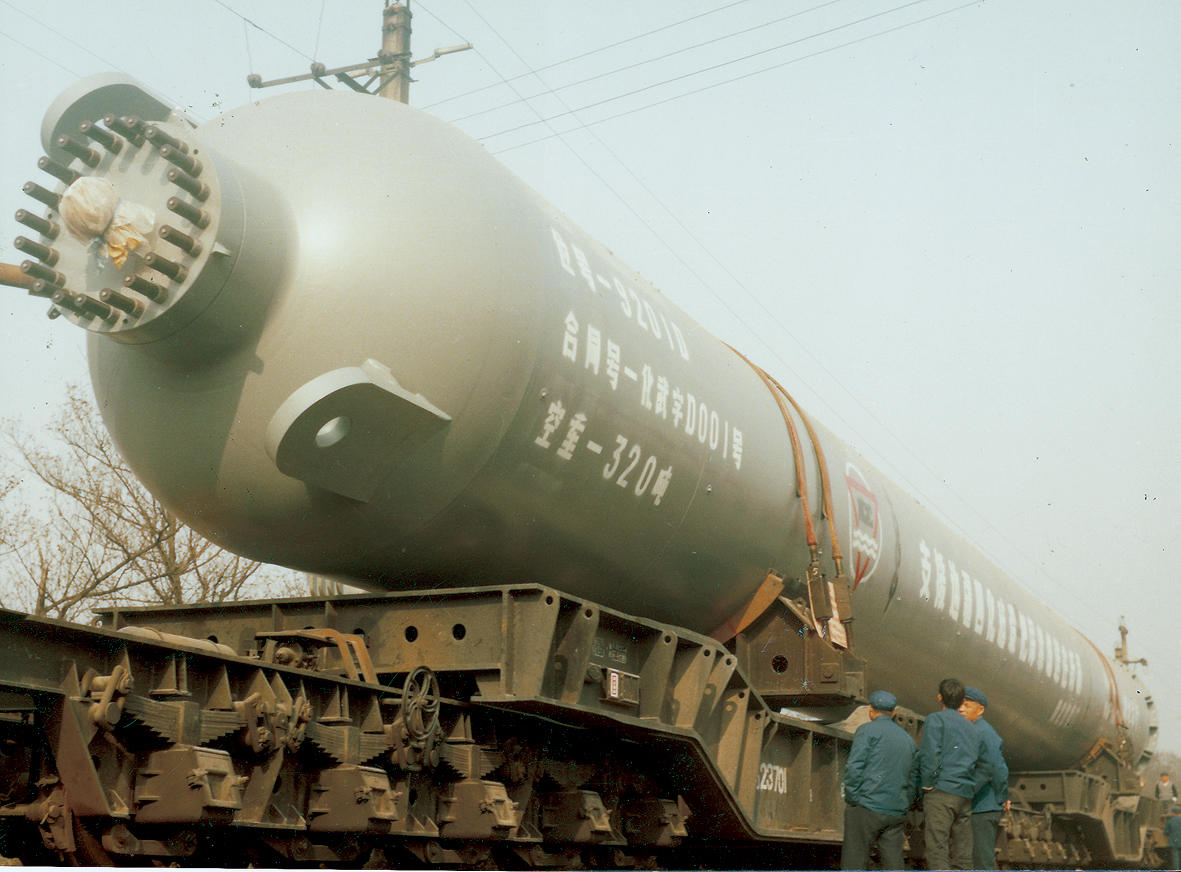
密封 密封對保證壓力容器正常運轉極為重要。壓力容器往往需要開啟作業,如更換內件、定期檢驗等,需要有可拆卸的端蓋,在端蓋與筒體聯接處就需要采用密封結構。密封結構由聯接件、緊固件和密封元件組成。圖3是常用的幾種高壓容器密封結構。密封按施加密封力的原理分為兩類:①強制式密封。完全依靠緊固件通過聯接件對密封元件施加密封壓力,以達到密封目的。這種密封是在容器未升壓前對密封元件施加很大的預緊力,其聯接件與緊固件的尺寸較大。②自緊式密封。主要依靠容器內介質的壓力壓緊密封元件,以達到密封目的。自緊式密封所需要的預緊力小,隨著容器操作壓力增高,密封比壓力也不斷增大,表現出優良的密封性能。
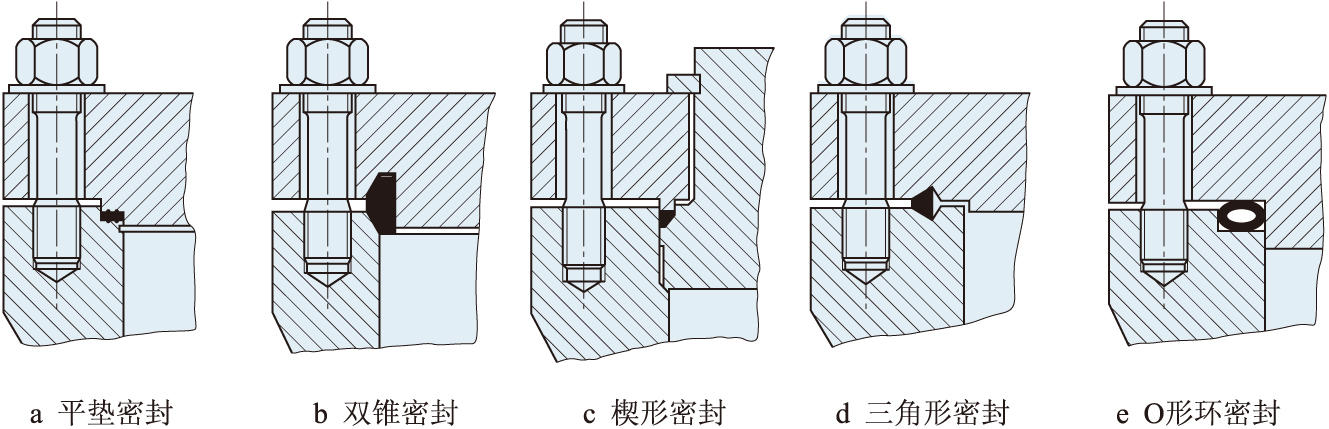
設計 壓力容器的設計通常包括:分析壓力容器的使用要求和操作條件,確定合理的結構形式;選擇合適的材料,規定制造工藝和質量要求;按容器可能發生的失效破壞形式,選擇恰當的失效判據和設計準則,確定適用的設計規范標準,再按規范標準要求進行設計或校核。
在各國制定的規范中,大多數仍將容器壁簡化成為均勻受力的薄膜進行處理,以薄膜應力來描述整個容器的應力水平。就圓筒形容器來說,若內部承受的壓力為p,平均直徑為d,筒壁厚度為δ,則沿切向的薄膜應力σt=p·d/2δ。規范要求應力σt應小於規定的許用應力。然而,容器各部位的實際應力狀態是很復雜的,如容器開孔邊緣的最大應力可達薄膜應力的2倍以上,但在設計容器時,因采用瞭較大的安全系數,整個容器的應力水平仍在安全范圍之內。為瞭避免容器發生脆性破壞,設計中除對材料要求具有足夠的強度(屈服點和抗拉強度)外,還要考慮沖擊韌性等要求。
在實際使用中,壓力容器的破壞除誤操作引起之外大多是由於腐蝕、疲勞、輻照和容器殼壁中存在過大的缺陷等原因造成的。因此,按常規的強度設計有時還不夠嚴密,還應區別不同使用情況進行特殊設計。如對高溫壓力容器必須按持久強度進行計算,因為在這種情況下溫度對材料的性能有重大的影響。對於操作壓力或溫度頻繁變動的壓力容器,應當進行疲勞分析設計。在存在缺陷的情況下,還應根據疲勞裂紋擴展理論對容器的使用壽命作出估算。對安全性要求極高的核電反應堆壓力容器,必須用有限元法和其他方法對容器各部位的應力進行較為精確的計算,並從許用應力、極限承載能力、安全條件和疲勞壽命等方面加以限制。為瞭防止反應堆壓力容器因存在過大的缺陷而破壞,在核壓力容器規范中開始采用斷裂力學判據,按容器中允許的缺陷采用安全系數來控制許用應力,目的在於籠統地估計許多難以確定的因素。若把各種與設計有關的參數按隨機變量作統計處理,求出其分佈規律,便可定量地求出壓力容器在運行中的失效概率,即可對壓力容器進行可靠性設計。
選材 很多壓力容器造成事故的重要原因之一是選用材料不當。如采用焊接性差的鋼材焊制壓力容器,容易在焊接接頭中產生裂縫,一些危險的裂紋會在使用中導致事故。有些鎳–鉻不銹鋼的壓力容器,常因鋼號或成分選用不當,在使用中發生晶間腐蝕、應力腐蝕等形式的破壞。選用鐵素體鋼制造低溫壓力容器時,如鋼的轉變溫度高於容器的工作溫度,則容器工作時容易發生脆性破壞。選材應滿足壓力容器操作條件要求,具有良好的加工工藝性,符合有關設計和材料標準的規定,並且經濟合理。大多數壓力容器由鋼制成,也有的壓力容器選用鋁、鈦及鎳基合金等有色金屬和玻璃鋼、預應力混凝土等非金屬材料制造。
選材不僅要考慮力學性能的要求,也需要考慮其耐蝕性。介質的成分、溫度和壓力等操作條件,往往對材料的耐蝕性有很大的影響。為瞭正確選用材料,必須瞭解準確的操作條件和材料在此條件下發生腐蝕破壞的形式。
質量檢驗 為保證壓力容器的安全使用,在制造時必須按照有關標準、規范對壓力容器的原材料和加工制造過程進行嚴格的質量檢驗。原材料與制造過程的檢驗主要包括以下內容:①原材料化學成分及力學性能的檢驗,必要時還應進行金相及腐蝕試驗。②壓力容器產品及其主要零部件形狀與尺寸偏差的檢驗。③采用產品焊接試板對產品焊接接頭力學性能進行檢驗。④采用射線、超聲、磁粉、滲透、渦流等無損檢測方法,對原材料、焊接接頭中可能存在的各種缺陷進行檢驗。⑤采用超壓的方法對壓力容器進行耐壓試驗,全面考核其強度。⑥采用氣密性試驗檢查密封部位是否泄漏。
定期檢驗與缺陷安全評定 為瞭保證壓力容器的安全運行,每隔一定時間必須對在用壓力容器進行定期檢驗。在用壓力容器定期檢驗分為外部檢查、內外部檢驗與耐壓試驗等。外部檢查以目視檢查為主,一般每年至少進行一次。內外部檢驗主要包括目視檢查、結構幾何尺寸檢查、厚度測定、材質檢驗、強度校核、無損檢測與安全附件檢驗等。根據檢驗結果確定在用壓力容器的安全狀況等級和內外部檢驗周期。大型關鍵性在用壓力容器經定期檢驗,發現大量難以修復的超標缺陷,使用單位因生產急需,可按照“合於使用”的原則,依據斷裂力學等方法通過缺陷安全評定來判定該壓力容器能否繼續投入運行。缺陷安全評定就是根據缺陷的性質、缺陷產生的原因以及缺陷的發展趨勢,對含缺陷壓力容器的安全性作出評價。
推薦書目
餘國琮. 化工容器及設備. 北京: 化學工業出版社, 1980.
國傢技術監督局. GB150-1998: 鋼制壓力容器. 北京: 中國標準出版社, 1998.