以拉力使坯料穿過各種形狀的錐形模孔,改變它的斷面,以獲得尺寸精確、表面光潔製品的塑性加工方法(圖1)。
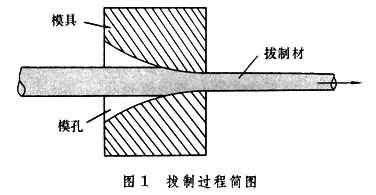
拔制材 包括管、絲、棒及異型斷面等規格。一般用軋制材、擠壓材或鍛材作坯料。生產毛細管時,也可用薄板沖壓成的杯形坯料。生產管和絲用的坯料形狀多數為圓形,而生產棒和異型材用的坯料有圓形、方形、扁形或異形。熱軋方式生產線材的最小直徑為5mm,而拔制絲的直徑可從6mm(粗絲)到0.001mm(極細絲);拔制管外徑一般從200mm到0.1mm,壁厚最薄到0.01mm,外徑與壁厚之比可達2000:1,長度可達100m。拔制棒材直徑一般為3~80mm。拔制還能生產各種復合材和品種日益增多的異型管材。
拔制工藝 一般包括打尖、熱處理、酸洗、塗潤滑劑、幹燥、拔制、矯直、切斷、塗油和包裝等主要工序。拔制工序因拔制管、絲、棒的規格和材質的不同而異。
冷拔過程中拔制應力必須小於模孔出口端金屬的屈服強度,以免金屬出現縮頸或拉斷。由於加工硬化,冷拔材的硬度、抗拉強度和屈服強度提高,塑性和韌性降低。
拔制是多道次、多工序和周期循環的工藝。由於受金屬抗拉強度的限制,冷拔材每道次的截面積減縮率一般小於40%,因此從原料到成品需經多道拔制。拔1~2道後需進行一次中間退火,退火產生的氧化皮經酸洗去除,同時塗上潤滑劑以利於拔制。棒材拔制時棒徑的變形量較小,隻有1~3mm,通常隻拔制1道,起定徑作用,所以被稱為“定徑材”。
拔制模具 拔制時使金屬變形的工具稱為模具。拔絲或棒時隻有外模具(拉模),金屬通過拉模中心的模孔進行拔制。拔管時還采用內模具(芯棒),以壓縮壁厚。
拔制力 從模孔拔出金屬所需拉力稱拔制力。在確定拔制的工藝參數和使用的設備時,拔制力是一個主要參數,影響拔制力的主要因素是金屬材質、變形量、工具形狀摩擦系數(潤滑劑)、拔制速度和後張力等。拔制時金屬在變形區內處於復雜的應力狀態,又必須考慮到材料的加工硬化,因此計算很復雜,一般計算拔制力都用簡單的經驗公式:
P=K(F0-F1)
式中 P為拔制力(kgf); F 0、 F 1為拔制前、後截面積( mm 2); K為拔制系數,取決於被拔制金屬材質和拔制方式,舉例如下表。 拔制系數舉例(kgf/mm²)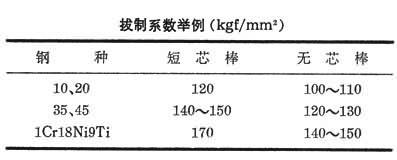
拔制設備 通常管棒材用直條拔制,廣泛采用鏈式拉拔機。拔制時用夾鉗小車鉗口咬住管棒材的頭部,小車尾鉤掛在傳動鏈條上外拔。拉拔機的拔制能力以許可的最大拔制力表示。常用的鏈式拉拔機的拔制力為0.5~150噸,額定拔速為每分鐘15~40m,拔制材的直徑為5~200mm,同時拔制根數為1~3根,拔制材最大長度為9~12m,管棒材拉拔機除鏈式以外,還有液壓式、齒條式、卷筒式和聯合式等。
拉絲機用絞盤拔制成盤線材。拉絲機的種類很多。隻拉1~2道的粗拉絲采用的單次拉絲機,有立式、臥式和倒立式三種。因線材盤重的增大,立式應用增多。多道的細拉絲采用的連續式拉絲機,有直線式、活套式、積線式(雙卷筒式和滑輪式)和水箱式等。帶有不停車上下線裝置的多模滑輪積線式拉絲機見圖2。
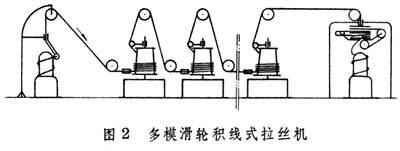
拔制生產的發展 近年來為瞭提高拔制效率,積極發展高速多線大噸位自動化冷拔機,拔管的最高速度達每分鐘135m,同時拔三根,最大拔制力有700噸。出現多模、連續、輥式、超聲和熱拔等新的拔制方法,拉絲的最高速度已達每分鐘2000m;還出現瞭水冷、等溫、反張力和熔融金屬直接拉絲等新方法。
現代化的拉絲生產中,還將熱處理和酸洗以及鍍層(先鍍後拔的鋼絲)等工序聯合組成多線開卷連續生產作業線,也可用機械去除鐵皮代替酸洗來拔制半成品鋼絲。
參考書目
王珂、王鳳翔編;《冷拔鋼材生產》,冶金工業出版社,北京,1981。