沒有固定加工順序和生產節拍,適應多品種小批量生產的機械製造系統。英文縮寫FMS。FMS的工藝基礎是成組技術,它按照成組的加工物件確定工藝過程,選擇相適應的數控機床或工件、工具等物料儲運系統。柔性製造系統以電腦為核心進行系統管理,用無人搬運車進行工件傳送,用數控技術實現自動化加工,用機器人進行自動裝卸,並具有監視切削狀態和精度、診斷和復原等功能,還能在一定範圍內完成一種零件加工到另一種零件加工的自動轉換。
發展概況 20世紀50年代,為瞭提高生產率,適用於大批量生產的組合機床和剛性自動線等專用設備得到很大發展。60年代,隨著小批量高精度加工產品的不斷增加,數控機床和加工中心進入瞭鼎盛時期。從70年代起,中小批量多品種的生產成為制造工業的生產特征。隨著科學技術的發展和產品更新換代速度的加快,中小批量產品的比例還有進一步增大的趨勢。這種情況迫使人們研制以適應中小批量多品種生產為主要目標的柔性制造系統。1963年美國研制成加工多種柴油機零件的數控自動線。1967年英國莫林公司首次提出完整的柔性制造系統的概念,並介紹瞭Molin-24系統的構想。隨後蘇聯、日本、聯邦德國都相繼研究出這類系統,如蘇聯於1983年公佈瞭加工軸類零件的柔性制造系統ГАСС和“設計制造綜合自動化”系統КАΠΡИ。
組成 柔性制造系統主要由多工位數控加工系統、自動化物料流輸送系統和計算機信息流控制系統組成。
多工位數控加工系統 傳統的數控系統的功能基本上靠固定的邏輯線路來實現,如需要擴充或改變功能則必須更改硬件邏輯,靈活性較差。柔性制造系統采用計算機控制的加工中心,這種數控裝置適應性強,能在硬件基本不變的情況下,通過修改軟件來改變或擴充其功能。加工中心一般都具有換刀裝置,工件一次裝夾後能連續地完成鉆、鏜、銑、鉸、锪等多種工序加工。如果用多臺加工中心組成柔性制造系統,便可以任意順序自動完成多種工件的多工位加工。
自動化物料流輸送系統 它包括存儲、輸送和搬運三個子系統,其功能為:自動地以任意順序存取工件和刀具;自動地按可變的自由節拍完成柔性制造系統中各個生產裝置的連接;自動地實現輸送裝置和加工設備之間的連接。柔性制造系統中的工件輸送系統與其他制造系統中的工件輸送系統有很大區別,它不是按固定節拍將工件從某一工位輸送到下一工位,而是既不按固定節拍又不按固定順序輸送工件,甚至有時是將幾種工件混雜在一起輸送。在這種系統中一般都設置儲料庫,以調節各個工位上所需加工時間的差異。工件輸送系統有直線輸送、環形輸送和閉環輸送三種基本類型。①直線輸送:輸送裝置沿機床一邊佈置,或從兩排機床中間通過。輸送工具可以是各種類型的傳送帶和運送小車,主要用於順序傳送。這種輸送裝置本身的存儲容量很小,常需設置中間儲料庫。②環形輸送:機床佈置在環形輸送線的外側。輸送工具除有各種類型的滾子傳送帶和運送小車外,還有架空單軌懸吊式輸送器。在封閉環形輸送線中常設置若幹支路,作為儲存工件和改變輸送線路之用,便於實現隨機傳送,具有較大的靈活性。③閉環輸送:整個傳送帶由許多隨行夾具和托板組成,借助托板上的編碼器能自動識別地址,從而可以任意編排工件的傳送順序。除這三種基本方式外,還有工業機器人,它主要用於中等尺寸的零件輸送和搬運。
計算機信息流控制系統 信息流控制系統的主要設備為計算機,與直接數控系統相似,通常具有A、B兩級或A、B、C三級計算機分級控制的結構形式。在A級中安排有大型通用計算機,並包含有零件自動編程系統,其主要職能是:將應用某種編程語言編寫的零件源程序處理成加工目的程序;完成管理控制,如分析原材料價格、記錄生產歷史資料、編制管理報告、綜合市場信息、核算經濟指標等。在B級中安排有中小型通用計算機,其主要職能是:將來自A級計算機的數據分發到各臺數控或計算機數控裝置和輸送裝置上去,並協調其工作,同時還對每臺機床進行生產狀態分析和判斷,並根據情況發出修改控制參數的指令。在 C級中安排有小型計算機、微型機或專用數控裝置,其主要職能是:執行來自上一級計算機的命令,直接控制機床加工,收集並處理檢測數據,向上級計算機反映各臺機床的生產狀態。
工作原理
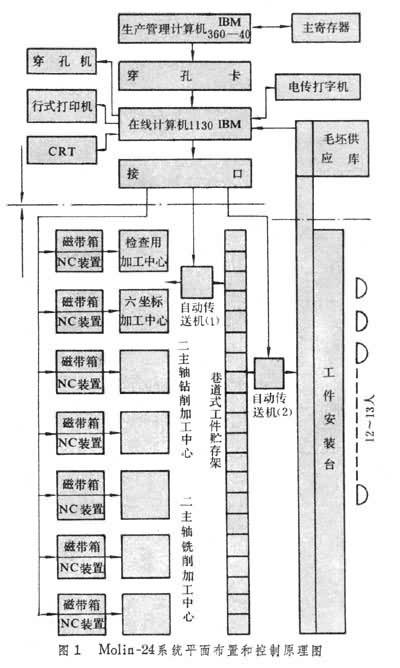
日本東芝公司自1983年起開始研制FMS。這種系統配備有兩臺計算機,用於自動安排作業、生產計劃和工藝管理,控制自動輸送裝置、自動監控裝置、自動化倉庫和15臺計算機數控加工中心(圖2、圖3)。
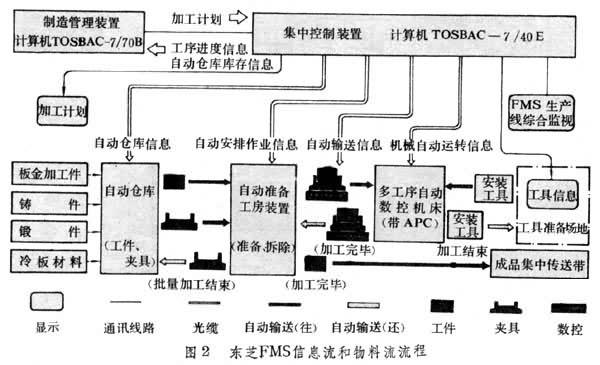
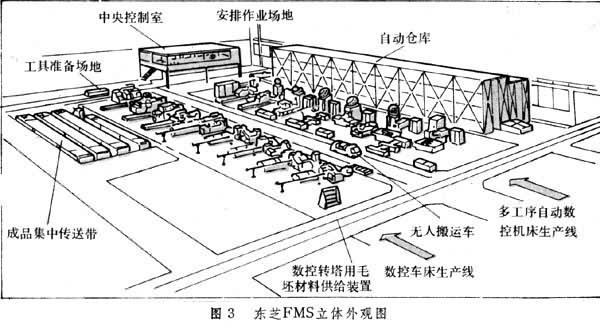